Alcast Company Can Be Fun For Everyone
Alcast Company Can Be Fun For Everyone
Blog Article
Alcast Company for Beginners
Table of ContentsAlcast Company Fundamentals ExplainedThe Ultimate Guide To Alcast CompanyThe Single Strategy To Use For Alcast CompanyAlcast Company Can Be Fun For AnyoneThe Best Guide To Alcast CompanyThe Buzz on Alcast CompanyThe smart Trick of Alcast Company That Nobody is Talking About

If you think that a functioned alloy might be the very best for your project, have a look at several of our articles that describe even more concerning details functioned alloys, such as Alloy 6061 and Alloy 6063. On the various other hand, if you assume an actors alloy would certainly be much better for you, you can find out more about some cast alloys in our Alloy 380 and Alloy 383 short articles (coming soon).
Unknown Facts About Alcast Company
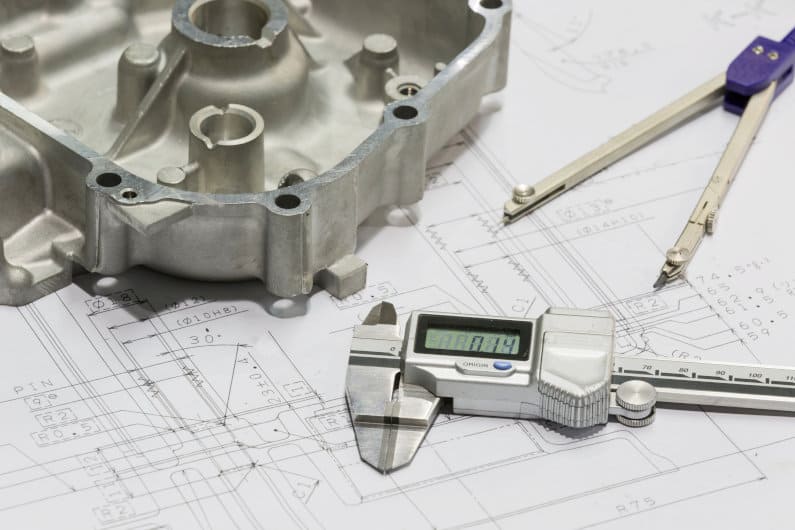
Having the experience and sector expertise to craft your spreadings for optimum manufacturing and top quality outcomes will improve the job. Producing aluminum castings requires a facility set of procedures to attain the best results. When deciding on a new aluminum foundry to companion with, guarantee they have substantial market experience and are experienced regarding all aspects of the aluminum spreading procedure: style, production, material analysis, and product testing.
(https://my.omsystem.com/members/a1castcmpny)The foundry needs to likewise have a proven track document of delivering remarkable items that satisfy or surpass customer expectations. Quality assurance needs to additionally go to the top of your listing when selecting a light weight aluminum factory. By functioning with a qualified factory that follows the criteria for quality assurance, you can protect the stability of your item and ensure it satisfies your specifications.
Some Known Details About Alcast Company
By selecting a firm that provides services that fulfill or exceed your product needs, you can be sure that your project will certainly be finished with the utmost precision and performance. Various components require various manufacturing methods to cast aluminum, such as sand casting or die spreading.
Pass away casting is the name offered to the process of developing complex steel components with usage of molds of the part, also understood as passes away. It produces even more parts than any various other procedure, with a high degree of precision and repeatability. There are three sub-processes that drop under the category of die casting: gravity pass away spreading (or long-term mold and mildew casting), low-pressure die casting and high-pressure die spreading.
Regardless of the sub-process, the die spreading procedure can be broken down right into 6 steps. After the pureness of the alloy is tested, passes away are created. To prepare the craves casting, it is essential that the dies are tidy, so that no residue from previous productions stay. After cleansing, the ejection lubrication is put on the die to guarantee a smooth release.
The pure metal, additionally referred to as ingot, is added to the furnace and maintained at the molten temperature level of the steel, which is then moved to the shot chamber and injected into the die (Foundry). The stress is after that kept as the steel strengthens. As soon as the metal solidifies, the cooling process starts
Examine This Report about Alcast Company
The thicker the wall of the part, the longer the cooling time as a result of the amount of interior metal that also needs to cool down. After the part is completely cooled, the die halves open and an ejection mechanism pushes the part out. Following the ejection, the die is closed for the next injection cycle.
The flash is the extra product that is cast throughout the process. This have to be trimmed off utilizing a trim tool to leave simply the primary part. Deburring eliminates the smaller pieces, called burrs, after the cutting process. The component is brightened, or burnished, to offer it a smooth coating.
Things about Alcast Company
Today, leading manufacturers utilize x-ray screening to see the entire interior of components without cutting right into them. To obtain to the finished product, there are 3 key alloys used as die spreading product to select from: zinc, light weight aluminum and magnesium.
Zinc is one of one of the most previously owned alloys for die casting as a result of its reduced cost of resources. It's likewise one of the stronger and stable metals. And also, it has superb electric and thermal conductivity. Its deterioration resistance likewise enables the components to be durable, and it is just one of the extra castable alloys as a result of its reduced melting point.
Rumored Buzz on Alcast Company
As pointed out, this alloy is one of more information one of the most generally utilized, yet manufactures will, sometimes, choose light weight aluminum over zinc due to light weight aluminum's manufacturing benefits. Light weight aluminum is highly affordable and among the much more functional alloys. Aluminum is made use of for a number of different items and industries anything from home window frameworks to aerospace materials.
Report this page